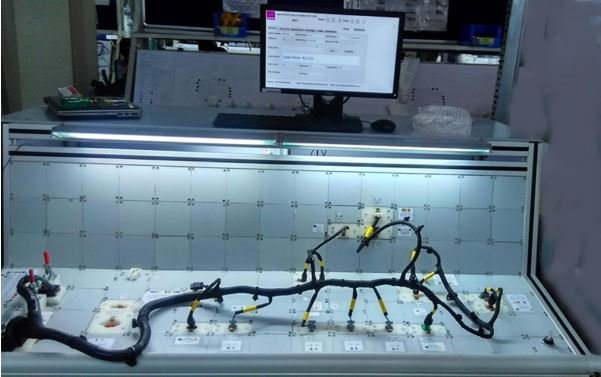
Automotive manufacturers in Nashik and Pune are increasingly focusing on improving efficiency and quality in their production lines. One of the most critical aspects of modern automotive manufacturing is ensuring that the vehicle’s electrical system functions properly, which relies heavily on the integrity of the wire harness. By implementing rigorous wire harness testing, factories in Nashik and Pune are reducing errors, improving efficiency, and ensuring safer, more reliable vehicles.
Why Wire Harness Testing is Crucial for Automotive Manufacturing
The wire harness acts as the central nervous system of a vehicle, connecting various electrical components such as the engine, lights, and sensors. A single error in the wiring can lead to vehicle malfunctions or, worse, safety hazards on the road. For this reason, manufacturers in Nashik and Pune are placing a strong emphasis on wire harness testing to ensure every vehicle leaves the production line without any electrical issues.
There are two main types of testing that are commonly used:
- Continuity Testing: This ensures that all wires in the harness are properly connected and that no breaks exist in the circuit.
- High-Voltage Testing: Also known as dielectric testing, this ensures the insulation around the wires can handle the electrical loads without breaking down or causing a short circuit.
How Wire Harness Testing Improves Manufacturing Efficiency
- Minimizing Rework: In large-scale automotive manufacturing facilities in Pune and Nashik, any error in the wire harness can result in costly rework, causing delays and adding unnecessary expense. Wire harness testing ensures that these errors are caught early in the production process, reducing the amount of rework required.
- Faster Assembly Processes: When manufacturers can be confident that each wire harness has passed its tests, the assembly process runs more smoothly. Testing automation allows for rapid verification, speeding up production timelines and enabling manufacturers to meet delivery schedules more consistently.
- Improved Product Quality: Consistent wire harness testing leads to higher product quality and fewer post-production issues. For manufacturers in Nashik and Pune, ensuring that the wire harness is fault-free means fewer warranty claims and returns due to electrical malfunctions.
Case Study: Enhancing Efficiency in Pune’s Automotive Manufacturing
One of Pune’s top automotive manufacturers faced a challenge in reducing downtime caused by faulty wire harnesses. After adopting an advanced wire harness testing system, the company saw a significant increase in production efficiency. By conducting both continuity and high-voltage testing on all wire harnesses before installation, the company reduced the number of post-assembly errors by 40%. This improvement not only enhanced overall efficiency but also reduced costs related to product rework and delays.
Challenges in Wire Harness Manufacturing and How Testing Solves Them
Automotive factories in Nashik and Pune face several challenges when it comes to ensuring wire harness quality:
- Complex Wiring Structures: Modern vehicles have increasingly complex electrical systems, and managing the wiring architecture can be challenging. Testing ensures that even complex wire harnesses are assembled correctly.
- Varying Vehicle Models: With each vehicle variant requiring different wire harness configurations, the risk of installing an incorrect harness increases. By using automated testing systems, manufacturers can ensure that the correct harness is always used for each model.
- Demand for Higher Safety Standards: Regulatory bodies in India and around the world are tightening safety standards for automotive manufacturers. Wire harness testing helps manufacturers in Pune and Nashik meet these stringent safety requirements by ensuring that electrical systems work as intended.
The Benefits of Automated Wire Harness Testing
The use of automated wire harness testing is transforming the way factories in Pune and Nashik approach quality control. Some of the key benefits include:
- Increased Accuracy: Automated testing eliminates human error and ensures that every wire harness is thoroughly checked for defects.
- Real-Time Error Detection: Automated systems can identify errors in real time, enabling manufacturers to correct issues immediately rather than after the vehicle has been assembled.
- Consistent Results: With automated testing, every wire harness is subjected to the same rigorous tests, ensuring that quality remains consistent across the board.
Conclusion
For automotive manufacturers in Nashik and Pune, wire harness testing is a critical step in improving production efficiency and ensuring product quality. By adopting automated testing systems, manufacturers can reduce rework, speed up production timelines, and maintain high safety standards for the vehicles they produce.
If your automotive factory in Pune or Nashik is looking to improve its production efficiency and enhance product quality, implementing a robust wire harness testing system can make all the difference. Contact us today to learn more about how our solutions can help your business succeed.