In manufacturing, every screw matters. Whether you’re assembling electronics, automotive components, appliances, or medical devices, improperly tightened fasteners can lead to product failures, safety risks, and costly service returns. Smart torque control tools are changing the game by offering a reliable, automated way to apply the perfect amount of torque—every single time.
Let’s dive into how torque control tools improve product quality, reduce defects, and bring a new level of precision to modern assembly lines.
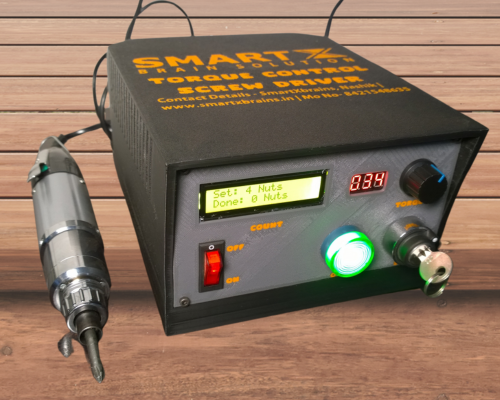
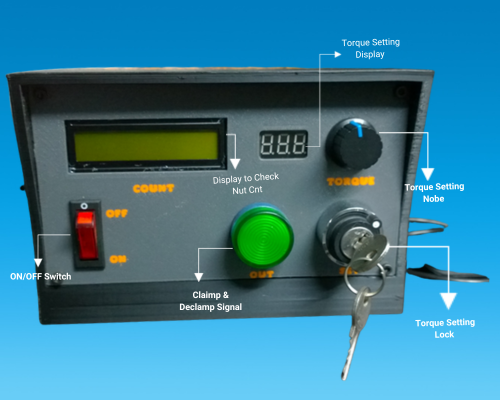
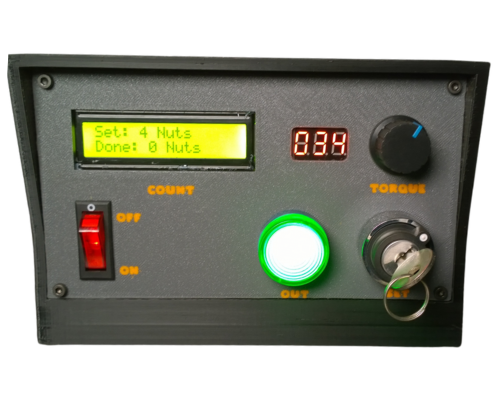
The Problem With Traditional Assembly Methods
In manual assembly, achieving consistent torque is a challenge. Operators may under-tighten or over-tighten fasteners due to fatigue, tool variation, or lack of torque feedback. This inconsistency can lead to:
- Loose screws that result in product failure
- Over-tightened screws that damage materials or strip threads
- Increased warranty claims and customer complaints
- Assembly line rework and downtime
What Are Torque Control Tools?
Torque control tools — also known as torque screwdrivers or torque guns — are specialized devices designed to apply a precise amount of torque to each fastener. These tools come with locking mechanisms, programmable settings, and often smart features like screw counting, error alerts, and data logging.
Benefits of Torque Locking and Precision Control
1. Improved Product Quality
By applying the exact torque required, these tools ensure fasteners are properly secured without damaging the material. This is critical for safety and longevity in sectors like automotive, electronics, and aerospace.
2. Reduced Service Issues
Loose or overtightened screws are among the top causes of service callbacks and product failures. Torque-controlled assembly helps eliminate these issues at the source, reducing field service costs and improving customer satisfaction.
3. Consistent Output Across Operators
No matter who’s on the shift, smart torque tools deliver uniform results. This reduces dependency on operator skill and minimizes human error, especially in high-speed production environments.
4. Data-Driven Assembly
Advanced torque tools can store and transmit torque data, making it easy to track performance, identify trends, and meet audit or compliance requirements.
5. Lower & Rework and Waste
With accurate torque application, there’s less need to recheck or redo work — saving time and materials, and boosting overall efficiency.
Benefits of Using Torque Control Guns with Poka-Yoke
- Enhanced Product Reliability
Ensures every device leaving the assembly line meets the highest quality standards. - Compliance With Industry Standards
Helps meet ISO, IPC, and other quality certifications required in electronics manufacturing. - Traceability and Data Logging
Smart tools can record each fastening operation, allowing traceability for audits and analysis. - Faster Operator Training
Intuitive systems reduce the learning curve for new operators, improving consistency across shifts. - Cost Savings
By reducing rework, warranty claims, and defect rates, these tools pay for themselves over time.
Where These Tools are Used
- Electronics assembly (mobiles, laptops, circuit boards)
- Automotive production (dashboard assembly, engine components)
- Home appliances (fan motors, washing machines)
- Medical device manufacturing
- Industrial machinery assembly
Conclusion
Smart torque control tools aren’t just tools — they’re quality assurance systems. By preventing loose or over-tightened screws, these devices protect your product integrity, reduce rework, and boost your brand’s reputation. For any manufacturer aiming for zero-defect assembly, torque locking and precision control are not optional — they’re essential.