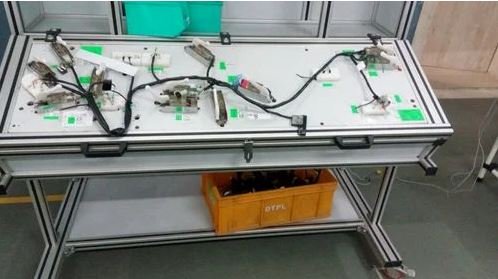
As automotive manufacturing grows rapidly in industrial hubs like Nashik and Pune, the need for high-quality components becomes essential to ensure vehicle safety and performance. One critical component in modern vehicles is the wire harness, responsible for connecting and powering various electrical systems. To ensure these systems work efficiently, conducting wire harness continuity testing has become a vital part of the manufacturing process.
What is Wire Harness Continuity Testing?
Wire harness continuity testing is a procedure used to verify the integrity of the electrical connections within the wire harness. It ensures that each wire is correctly connected and that no breaks or defects exist in the electrical path. For automotive manufacturers in Nashik and Pune, this testing is crucial to ensure that vehicles leaving the assembly line meet the highest safety and performance standards.
Why is Continuity Testing Important for Automotive Manufacturers?
- Preventing Electrical Failures: Automotive manufacturers in Nashik and Pune rely on wire harness continuity testing to prevent electrical failures. Without proper testing, a faulty wire harness can lead to serious issues such as malfunctions in lighting systems, airbags, and other critical components.
- Enhancing Vehicle Safety: Safety is paramount in the automotive industry, and a properly functioning wire harness is essential to ensure all electrical systems operate as intended. By conducting continuity tests, manufacturers can guarantee that the wire harness will perform without error, minimizing risks on the road.
- Maintaining Product Quality: Ensuring the wire harness meets exact specifications and is free from defects helps maintain the overall quality of the vehicle. Continuity testing ensures that all electrical connections are correctly established, preventing issues during vehicle operation.
How Continuity Testing Works in Wire Harness Manufacturing
The process of wire harness continuity testing involves several steps that ensure each electrical connection is intact and functional:
- Step 1: Connection Verification: Using automated testing equipment, the continuity test checks whether each wire is correctly connected to its corresponding terminal, ensuring there are no gaps or improper connections.
- Step 2: Detecting Breaks in Wires: The test ensures there are no breaks or discontinuities in the wires that could interrupt electrical flow. If any discontinuity is detected, the harness is flagged for repair or replacement.
Step 3: Confirming Signal Flow: By sending an electrical signal through the wire harness, the system checks that the signal flows uninterrupted from start to finish, confirming the integrity of the wiring.
Case Study: Improving Quality Control in Nashik’s Automotive Sector
A leading automotive manufacturer in Nashik was facing challenges related to intermittent electrical failures in their vehicles. After integrating a wire harness continuity testing system, the company saw significant improvements in both product quality and safety. The continuity test allowed the manufacturer to catch wiring issues before the harnesses were installed in vehicles, resulting in a 30% reduction in post-production electrical failures.
Benefits of Wire Harness Testing for Automotive Factories in Pune
Automotive factories in Pune are increasingly turning to wire harness continuity testing as a part of their quality control processes. This testing is essential in achieving the high level of reliability expected by consumers and regulatory bodies. The benefits include:
- Early Detection of Defects: Detecting defects early in the manufacturing process reduces costly rework and ensures that only fully functional wire harnesses are installed in vehicles.
- Enhanced Manufacturing Efficiency: Automated continuity testing speeds up the testing process, allowing manufacturers to quickly verify each wire harness before it proceeds to assembly.
Compliance with Industry Standards: By implementing rigorous continuity testing, manufacturers can ensure their vehicles comply with automotive industry standards for electrical systems, enhancing their reputation for quality and safety.
Conclusion
For automotive manufacturers in Nashik and Pune, wire harness continuity testing is not just an essential part of the production process, but also a critical factor in ensuring vehicle safety and quality. By adopting automated continuity testing systems, manufacturers can minimize defects, reduce costs, and improve the overall reliability of their vehicles.
If your automotive manufacturing plant in Nashik or Pune is looking to improve its wire harness quality, contact us today to learn more about our wire harness continuity testing solutions.