In India’s rapidly evolving manufacturing landscape, efficiency and precision are no longer optional — they are essential. This is especially true in assembly operations, where even a single missed or over-tightened screw can disrupt the supply chain or damage a brand’s reputation.
This case study explores how one Indian electronics manufacturer transformed its production line by adopting SmartxBrains Screw Counting Guns — a smart solution designed to eliminate fastening errors and improve productivity.
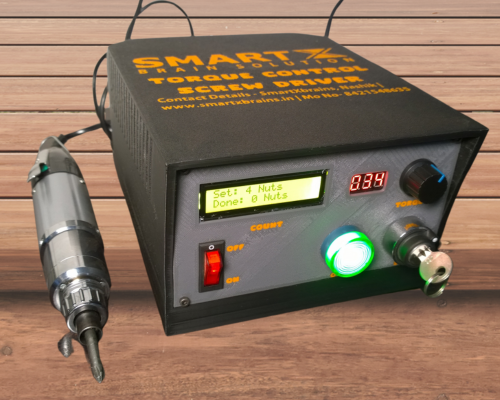
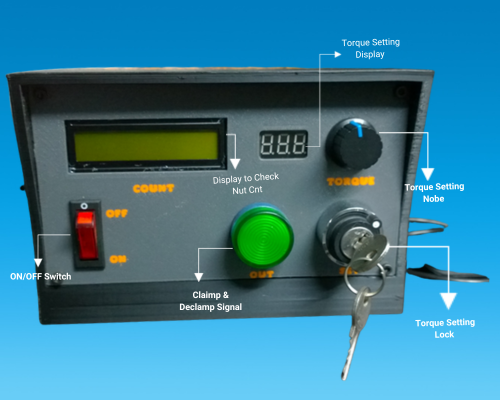
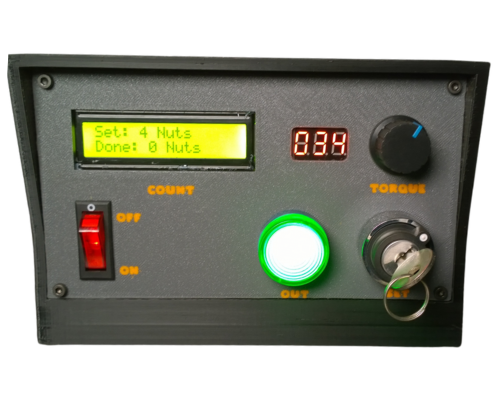
The Challenge
A mid-sized consumer electronics company based in Pune faced recurring problems on its assembly line:
- Missed screws in final product inspections
- Rework and downtime due to inconsistent screw fastening
- Increased warranty claims caused by loose or over-tightened fasteners
- Lack of traceability and manual quality checks slowing down throughput
Despite training efforts, human error continued to affect line performance and product quality. Management began looking for a technology-driven solution to reduce these issues and automate the fastening process.
The Solution: Smartxbrains Screw Counting Guns
After evaluating several options, the company invested in SmartxBrains Screw Counting Electric Screwdrivers. These advanced tools were chosen for their:
- Screw counting functionality to ensure no fastener is missed
- Torque precision control to prevent over-tightening
- Real-time alerts and lockout features for mistake-proofing (Poka-Yoke)
- Data logging capabilities for traceability and process auditing
The tools were integrated into two key assembly lines: PCB fixing and final product casing.
Implementation Highlights
- Training time reduced by 40% due to the tool’s intuitive interface and built-in guidance system
- Operators received immediate feedback on their screwdriving accuracy
- Supervisors monitored progress digitally, eliminating the need for manual checks
- Downtime dropped by 30%, thanks to early error detection and fewer defects
Results After 3 Months
Assembly Accuracy Improved by 95%
Rework Cases Reduced by 80%
Daily Output Increased by 25%
Zero missed screws recorded in random quality audits
Improved employee morale due to fewer errors and tool-guided confidence.