Introduction
In today’s competitive market, industries must prioritize efficiency, adaptability, and cost-effectiveness. Traditional metal jigs, though reliable, often fall short in meeting these demands due to high production costs, long lead times, and limited customizability. This is where 3D printed jigs step in. Combining cost-efficiency with unparalleled customization, 3D printed jigs are transforming manufacturing processes across industries. This blog explores why 3D printed jigs are the go-to solution for modern businesses aiming to stay ahead.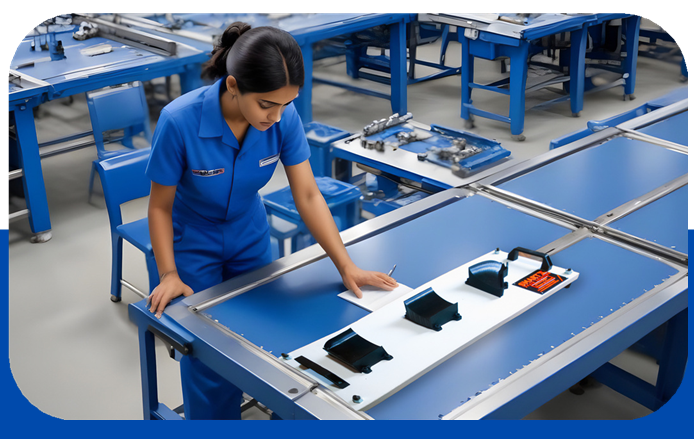
Why 3D Printed Jigs Stand Out
Lower Costs:
- Material Savings: Additive manufacturing uses only the necessary material, reducing waste.
- Reduced Manufacturing Costs: Eliminates the need for expensive molds and tooling.
- Lower Transportation Costs: Lightweight designs make shipping and handling more economical.
- Material Savings: Additive manufacturing uses only the necessary material, reducing waste.
Tailored Designs:
- Intricate Profiles: 3D printing enables the creation of complex geometries that traditional methods can’t achieve.
- Ergonomic Solutions: Jigs can be customized for operator comfort and specific task requirements, enhancing efficiency.
Rapid Production:
- Faster Turnaround Times: No need for lengthy tooling setups; designs can be printed directly from digital files.
- On-Demand Manufacturing: Businesses can quickly produce jigs as needed, reducing inventory costs.
Conclusion
3D printed jigs represent a significant leap forward for industries striving to balance efficiency, customization, and cost-effectiveness. By adopting this innovative technology, businesses can streamline their operations, reduce overhead expenses, and respond swiftly to evolving market demands. As 3D printing continues to advance, the benefits of these versatile jigs will only grow, making them an essential tool for industries seeking a competitive edge in the modern era.